I am starting to try and build a Vulcan Beam Engine from raw stock and not castings.
Full picture gallery: Vulcan Beam Engine Photo Gallery
The first step was to convert the plans (purchased) into a CAD program to see how things fit together. So far I have just got the standards, beam created in CAD.
To try and see if not using casting is possible I am going to try and fabricate the beam from raw stock and silver solder bits together.
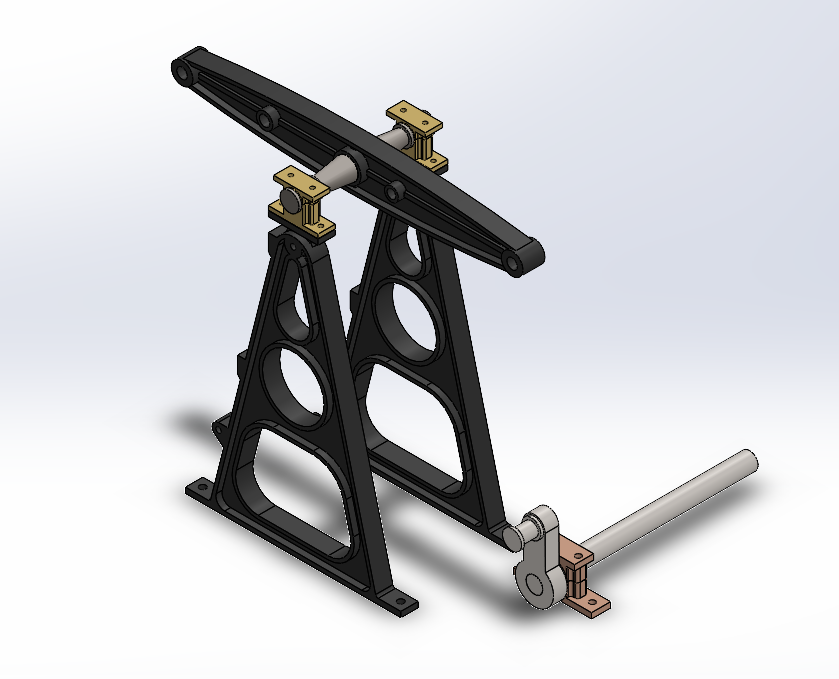
First step was to mark out for the holes and main features. Then to drill 3mm holes for registration.

Then to use the bandsaw to rough cut the webs. First using an offcut of 4mm aluminium to make a rudimentary table for my horizontal bandsaw.
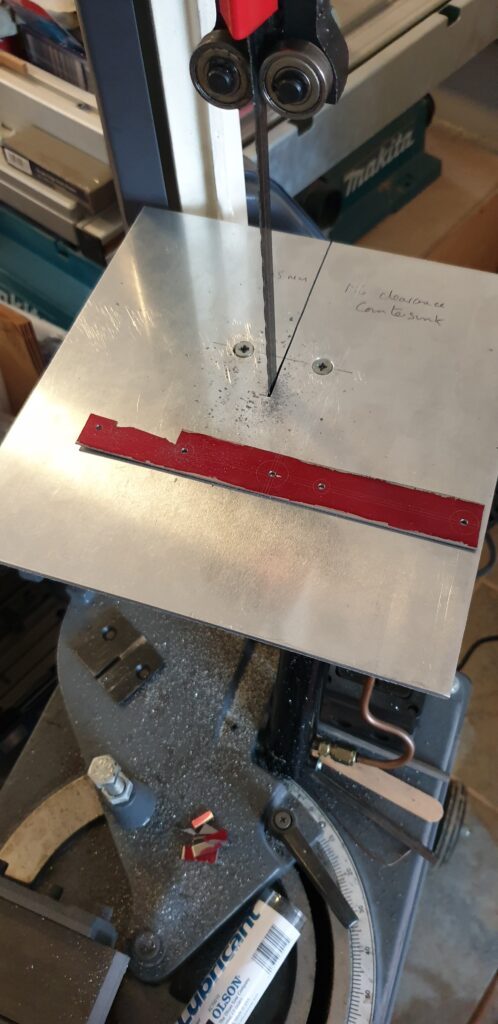
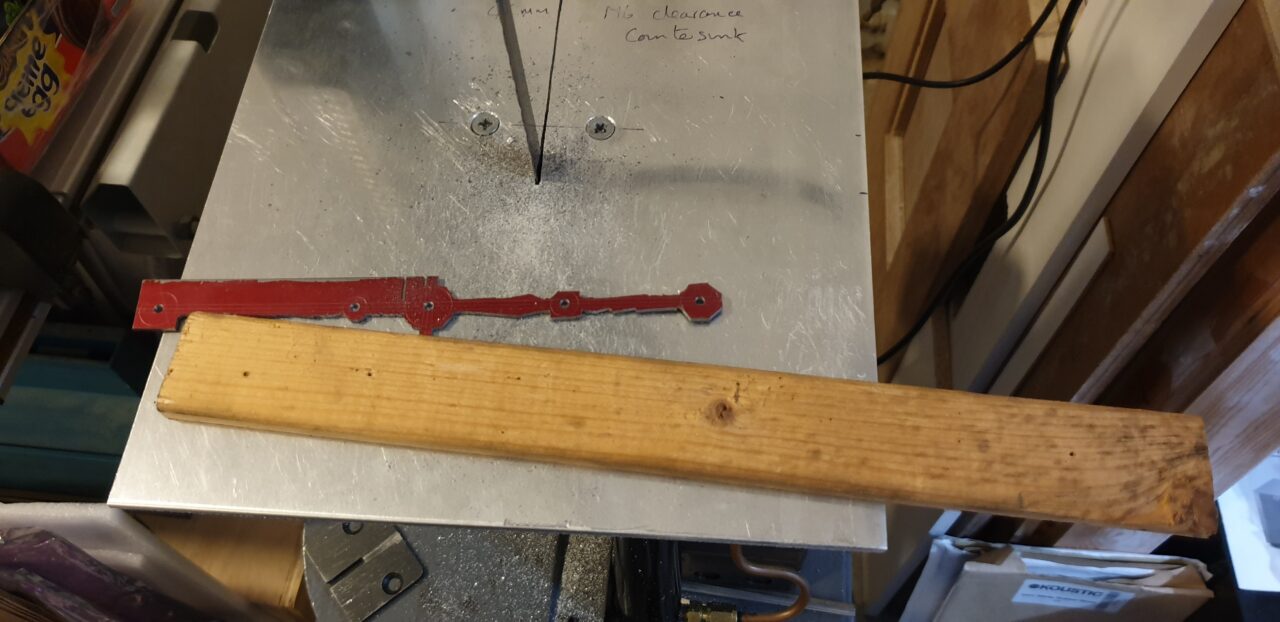
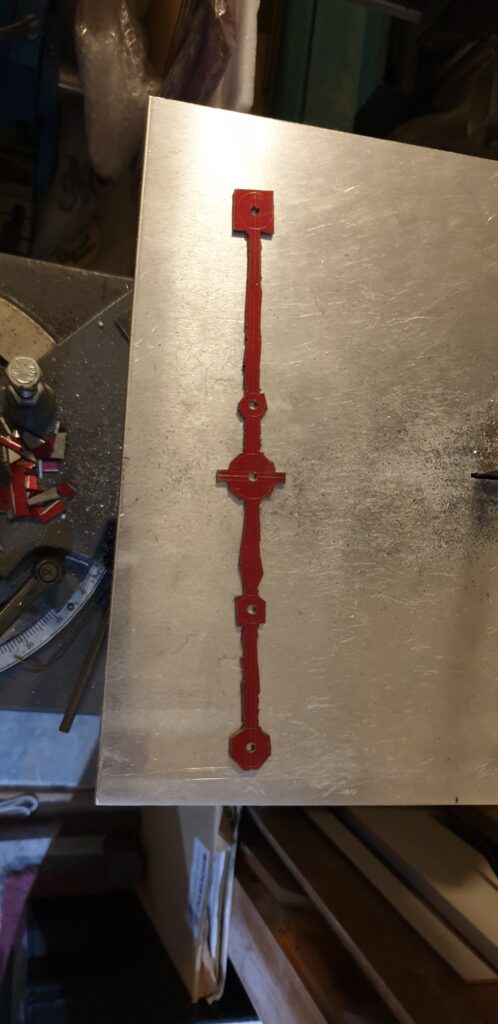
Now to use a 1″ belt sander to get to the line where possible. Then back to files.
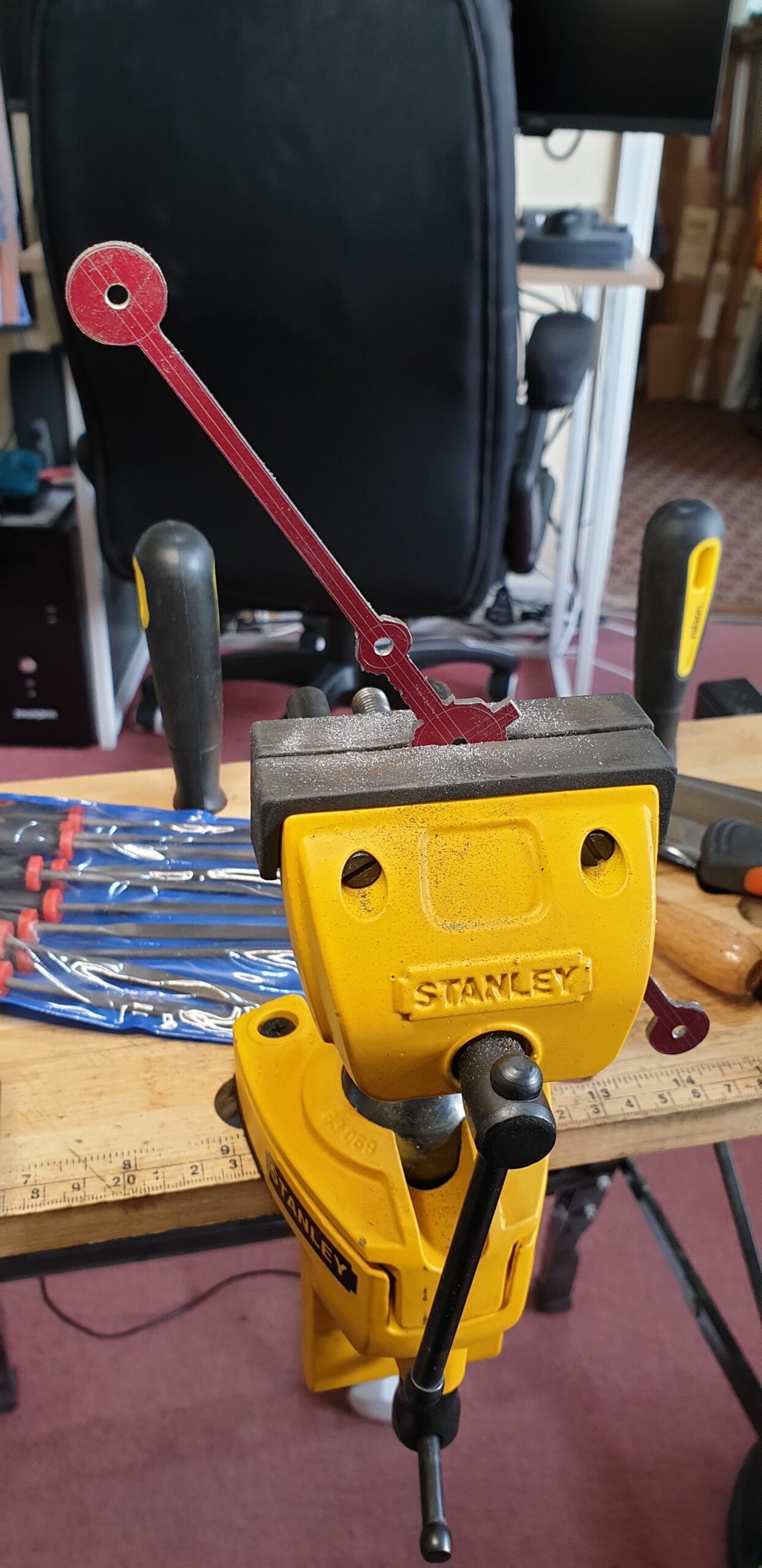
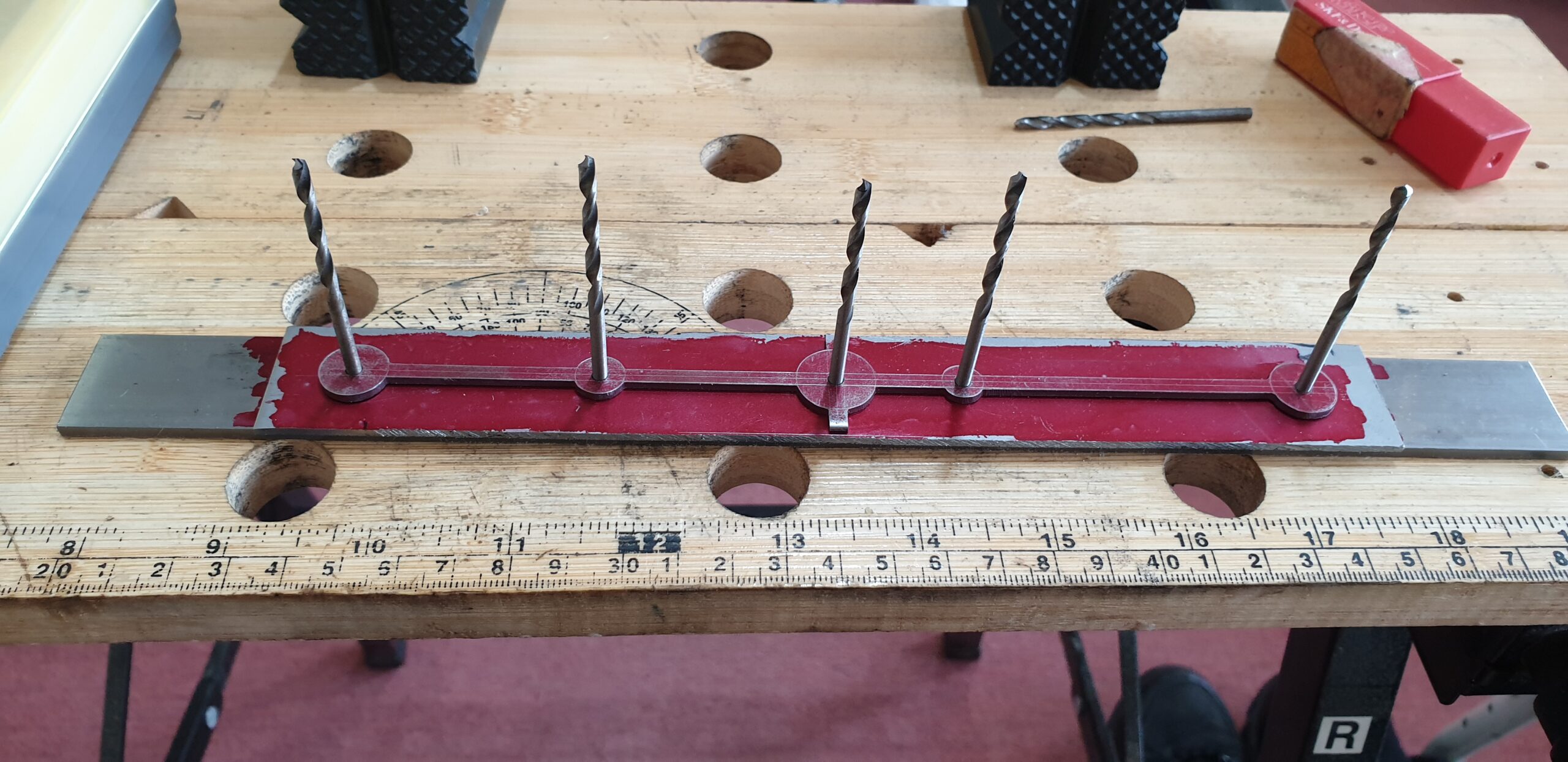
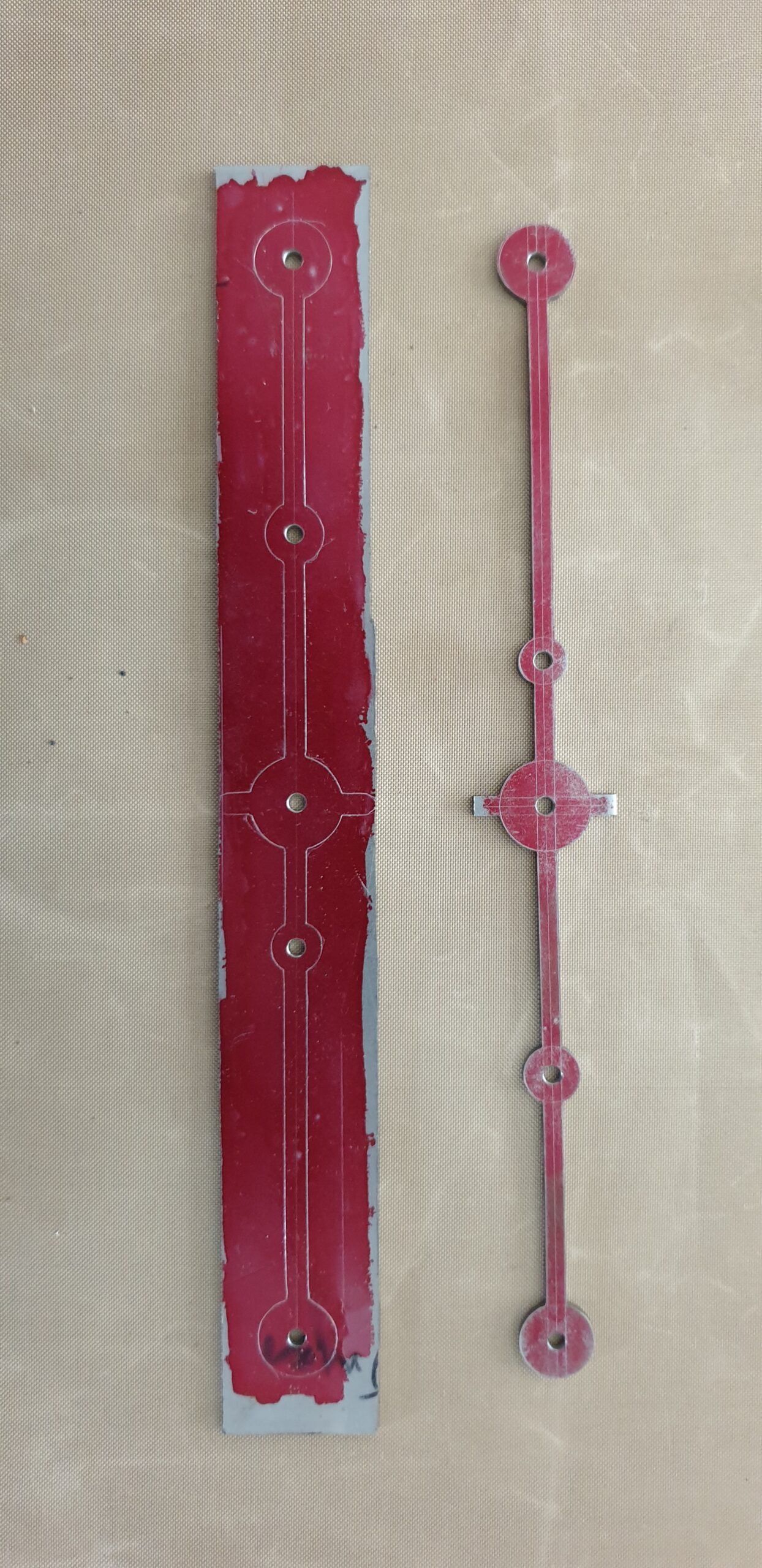
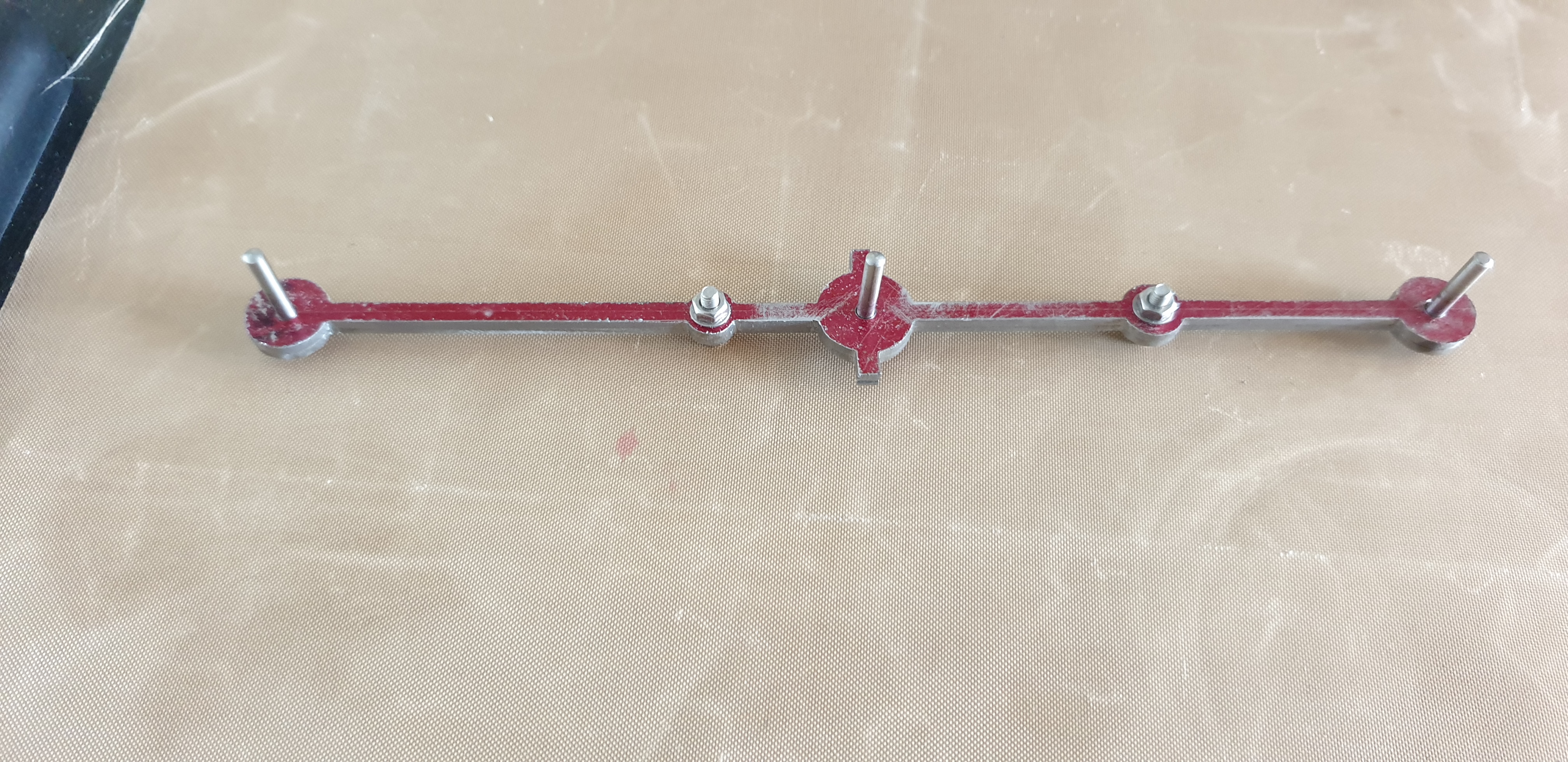
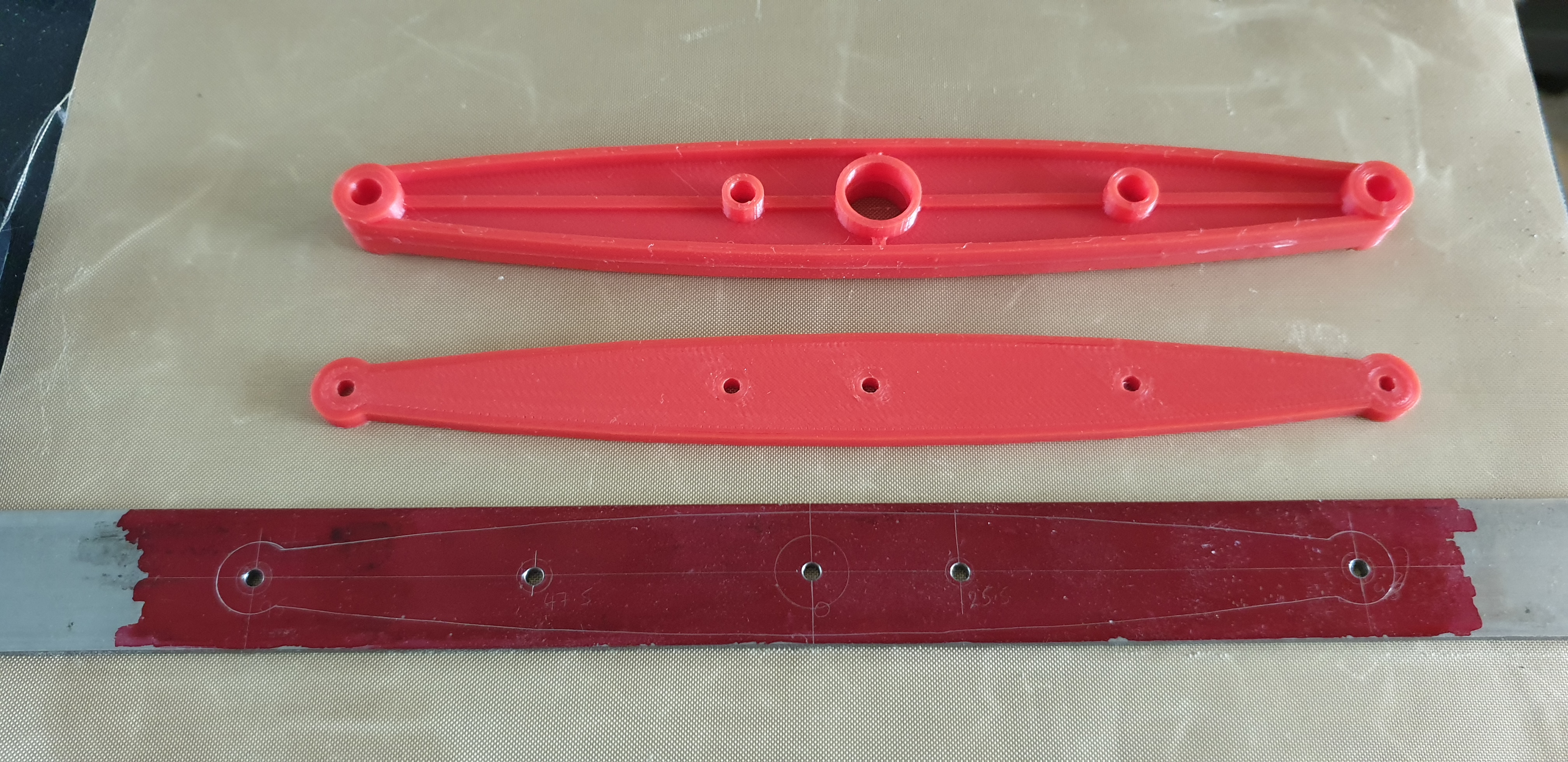
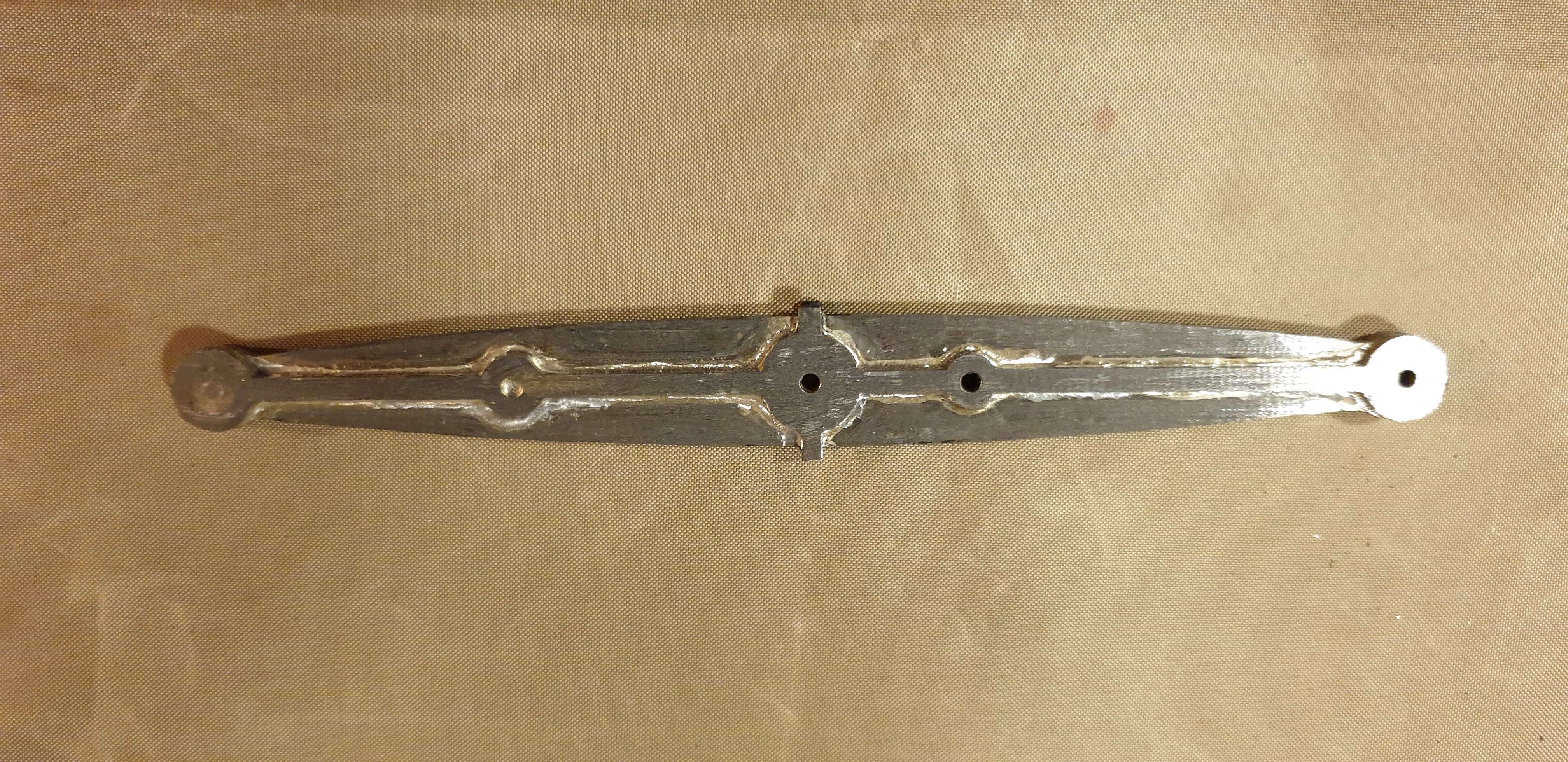
For the silver soldering I was trying to use an OxyTurbo Mapp/Oxygen torch with a small nozzle. However I think that this was too hot and actually was burning the flux before it could do its work. For the second side (the one shown above) I just used a normal propane torch which worked a lot better for this size of part. For the flux I first tried the easyflow flux, however I suspect that this was not good enough for the longer duration the soldering took. I then tried Tenacity 5A but didn’t like that due to the colour and not seeing if it was working. So for the second side I tried just tenacity 5 and this worked better for me.
However, I need a lot more practice in silver soldering and trying different torches. So I have made the choice to buy the castings.
Starting with the casting for the flywheel. This was not a very good casting and may not work, but I will give it a go. It is also at the max limit of my lathe.
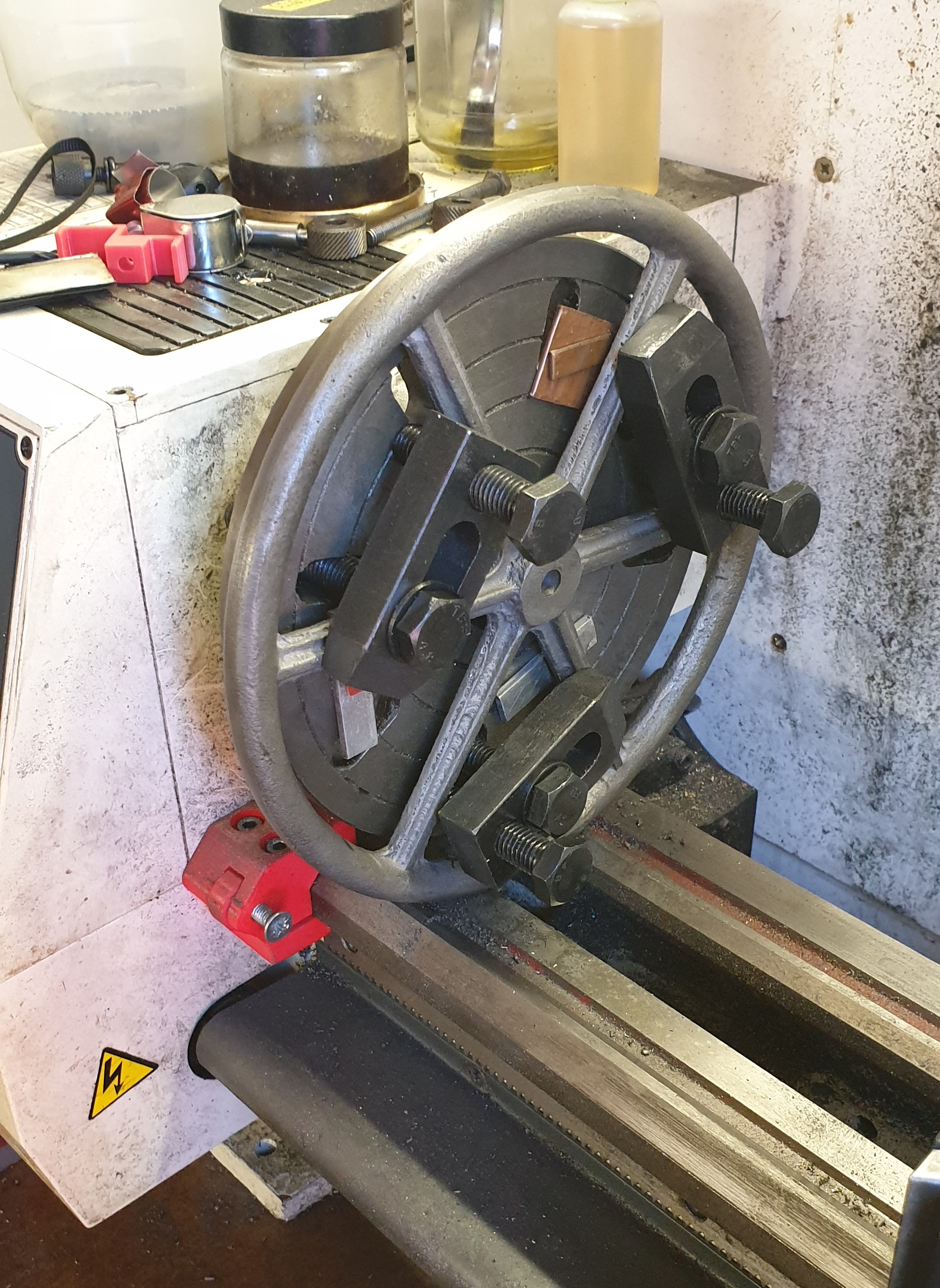
I also think that I need to make some more mounting straps etc.